PROCEDURE / APPLICATION
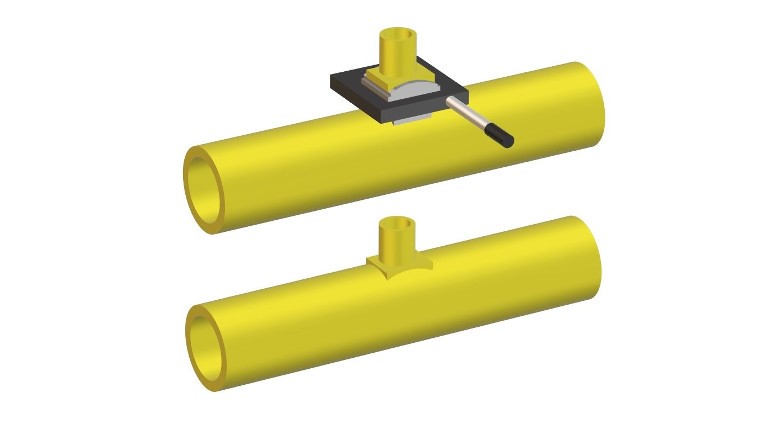
The saddle-fusion procedure involves melting the concave surface of the base of a saddle fitting, while simultaneously melting a matching pattern
on the surface of the pipe, bringing the two melted surfaces together and allowing the joint to cool while maintaining the appropriate applied force.
An appropriately sized saddle fusion machine is used to clamp the pipe main and the fitting, align the parts and apply the specified fusion force.
The Plastics Pipe Institute recommends that saddle fusion joints be made only with a mechanical assist tool, providing proper alignment and force control, unless hand fusion is expressly allowed by the pipe and/or fitting manufacturer.
Apparatus for saddle fusion
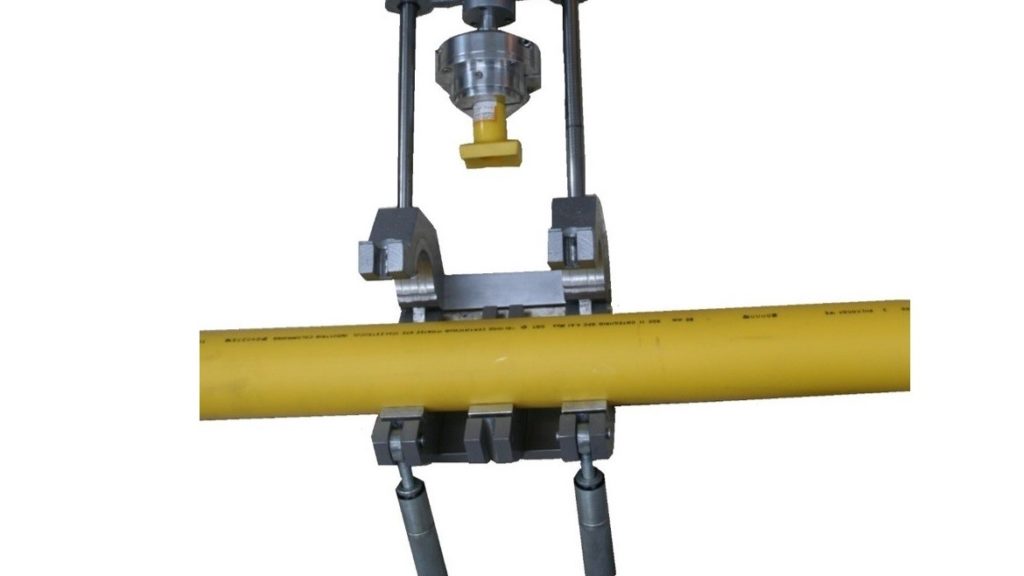
Saddle fusion Tool
This tool clamps to the main, rounding and supporting the main for good alignment between the pipe and fitting. It holds the fitting, in correct alignment to the main. It also applies and indicates the proper force during the fusion process. A support or bolster is clamped to IPS 6 in. (168 mm) and smaller main pipe opposite the fitting installation area to support the main and assist in rounding the pipe.
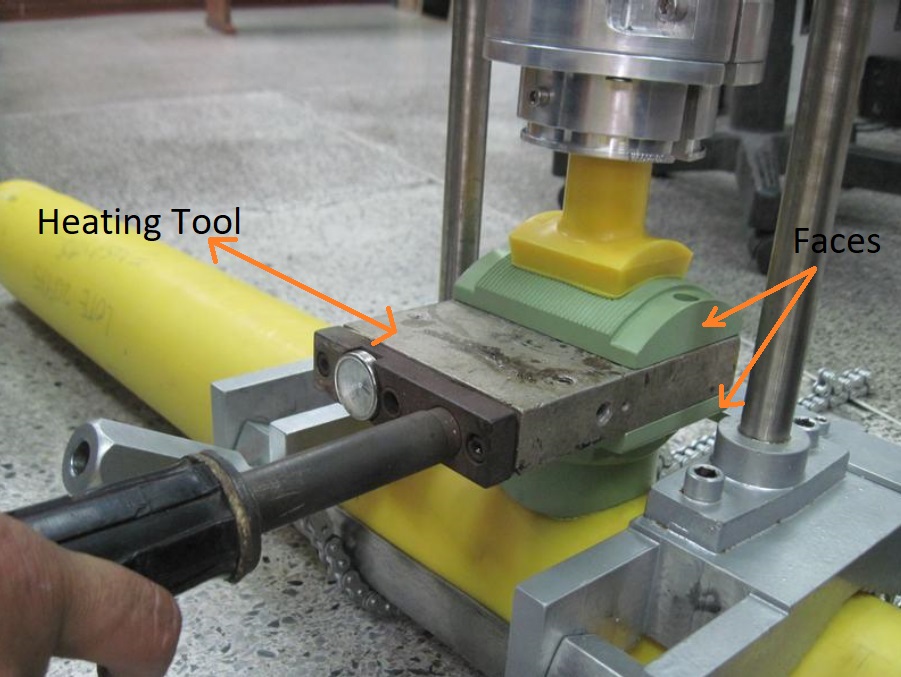
Heating tool and faces
This electrical tool shall have sufficient wattage and control to maintain the specified surface temperature of the tool faces. The serrated or smooth faces are matched sets, by pipe size, of concave and convex blocks, which bolt or clamp onto a flat heating tool. The heating faces are coated with a non-stick material to prevent sticking to the pipe or fitting surfaces.
Saddle Fusion Terminology:
- Initial Heat (Bead-up)—The heating step used to develop an initial melt bead on the main pipe.
- Initial Heat Force (Bead-up Force)—The force (lb) applied to establish an initial melt pattern on the main pipe. The Initial Heat Force is determined by multiplying the fitting base area (in.2) by the initial interfacial pressure 60 (lb/in.2).
- Heat Soak Force—The force (lb) applied after an initial melt pattern is established on the main pipe. The Heat
Soak Force is the minimum force (essentially zero pounds) that ensures that the fitting, heater and main stay in contact with each other. - Fusion Force—The force (lb) applied to establish the fusion bond between the fitting and the pipe. The fusion Force is determined by multiplying the fitting projected base area (in.2) by the fusion interfacial pressure 30 (lb/in.2).
- Total Heat Time—Atime that starts when the heater is placed on the main pipe and initial heat force is applied and ends when the heater is removed.
- Cool Time—The time required to cool the joint to approximately 120°F (49°C). The fusion force must be maintained for 5 min on IPS 11⁄4 in. (42 mm) or 10 min for all other main sizes, after which the saddle fusion equipment can be removed. The joint must be allowed to cool undisturbed for an additional 30 min before tapping the main or joining to the branch saddle.
- Interfacial Area for Rectangular Base Fittings—The major width times the major length of the saddle base, without taking into account the curvature of the base or sides, minus the area of the hole in the center of the base.
- Interfacial Area for Round Base Fittings—The radius of the saddle base squared times p (3.1416) without taking into account the curvature of the base or sides, minus the area of the hole in the center of the base.
- Fitting Label—The initial heat force, heat soak force and the fusion force will be listed on a fitting label in the lower right hand corner of the fitting for some manufacturer’s saddle fusion fittings. This will eliminate the need to calculate the fusion forces in the field (for example, 180/0/90). The label is not mandatory, therefore the heat and fusion forces need to be calculated if the label is not present.
Setup
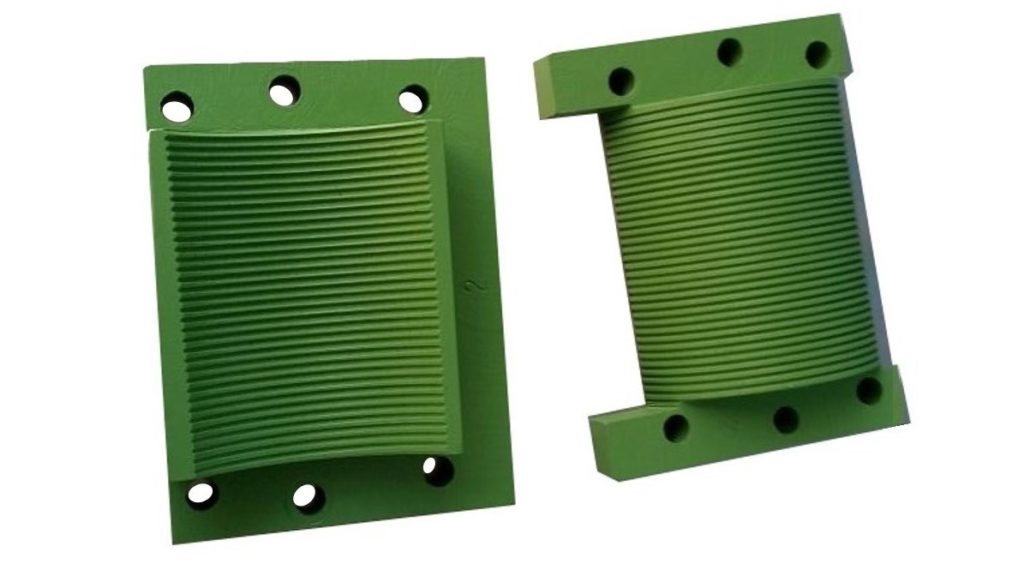
- Select and install the proper heating tool faces to the
heating tool based on the main size and fitting base size.
Consult the pipe, fitting or equipment manufacturer’s recommendations.
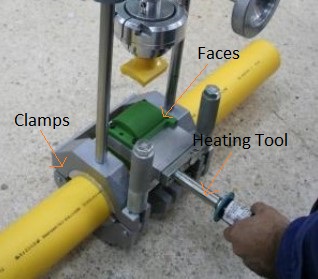
2. Plug in the heating tool and bring the heating tool face surfaces to 490 to 510°F (254 to 266°C). A pyrometer or other surface temperature measuring device is used to determine and periodically check the heating tool surface temperature.
3. Install the proper clamps in the Saddle Fusion Tool for the main size to be fused. Install the proper fitting clamp for the fitting to be joined. Consult the pipe, fitting or equipment manufacturer’s recommendations.
Procedure
ASTM INTERNATIONAL Designation: F2620 – 11
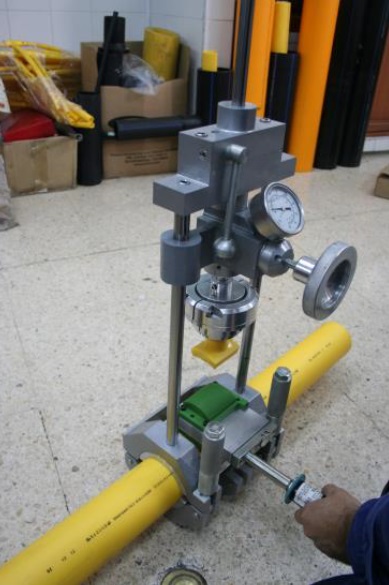
- Install the Saddle Fusion Tool on the main according
to the manufacturer’s instructions. The tool should be centered over a clean, dry location where the fitting will be fused. Secure the tool to the main. A main bolster or support is recommended under the pipe on IPS 6 in. (168 mm) and smaller main pipe sizes.
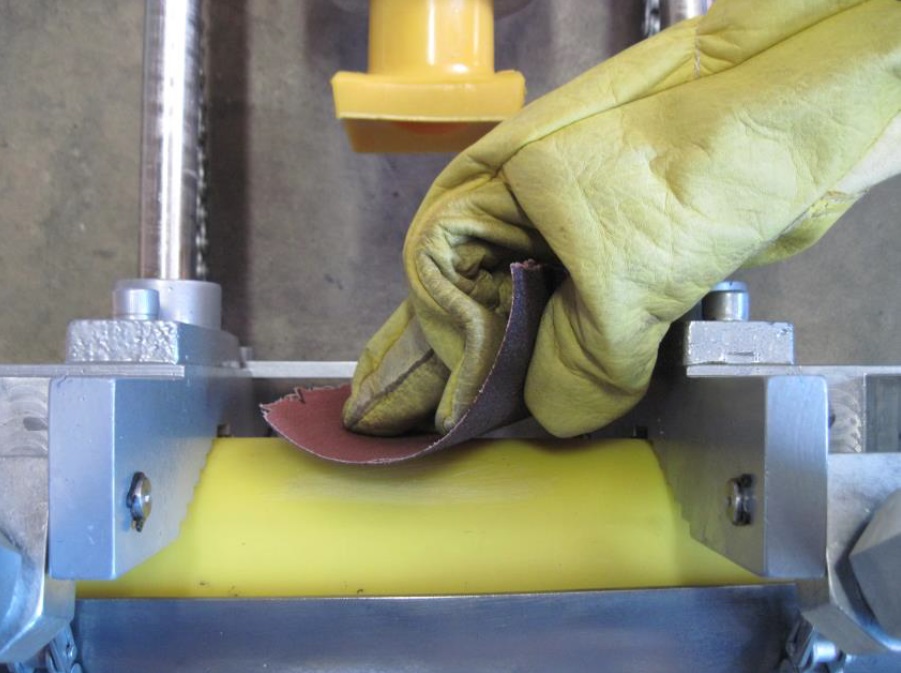
2. Abrade or scrape the surface of the main, where the fitting will be joined, approximately 0.007 in. (.178mm) deep to remove any oxidation or contamination. This can be done before or after the Tool is attached to the main. The abraded/ scraped area must be larger than the area covered by the fitting base.
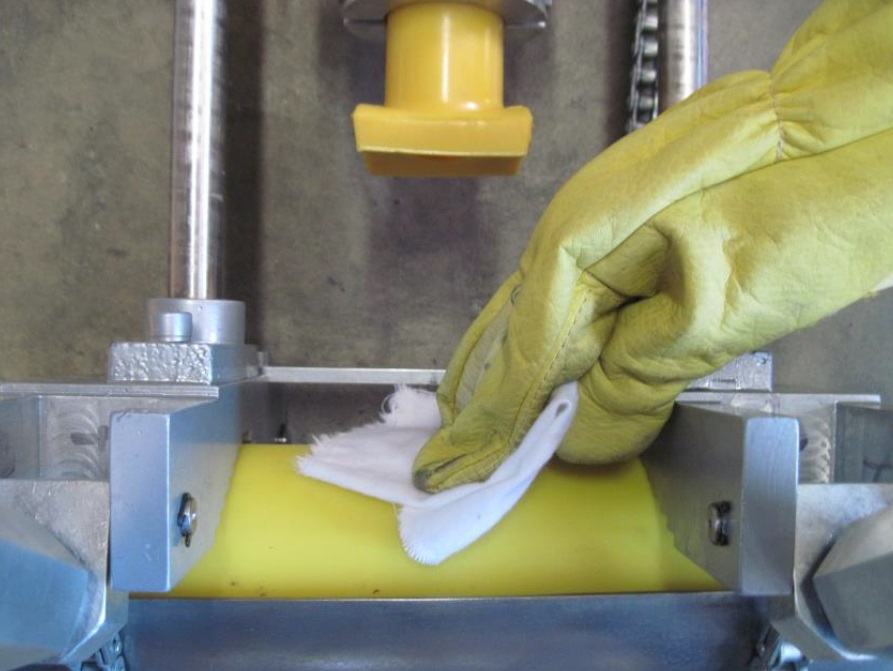
3. It is important that the pipe surface be free from any type of contaminates that may be spread before the scraping or abrading process begins. Marks can be made on the outer surface of the pipe to aid in visual indication of abrading/ scraping coverage, however the marks should be made with a non-petroleum based fast drying marker. After abrading/ scraping, clean the pipe or fitting ends with a clean dry lint free cloth. All markings on the pipe surface should be removed
before beginning the heat cycle.
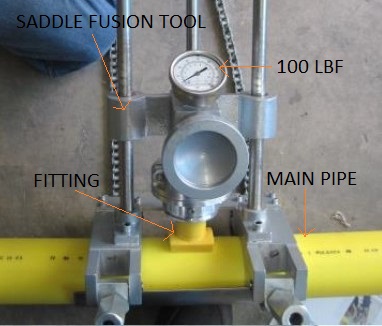
4. If the fitting is not protected in a clean plastic bag, abrade the fusion surface of the fitting with 50 to 60 grit utility cloth; remove all dust and residue with a clean dry lint free cloth. Insert the fitting in the Saddle Fusion Tool loosely. Using the Saddle Fusion Tool, move the fitting base against the main pipe and apply about 100 lbf to seat the fitting. Secure the fitting in the Saddle Fusion Tool.
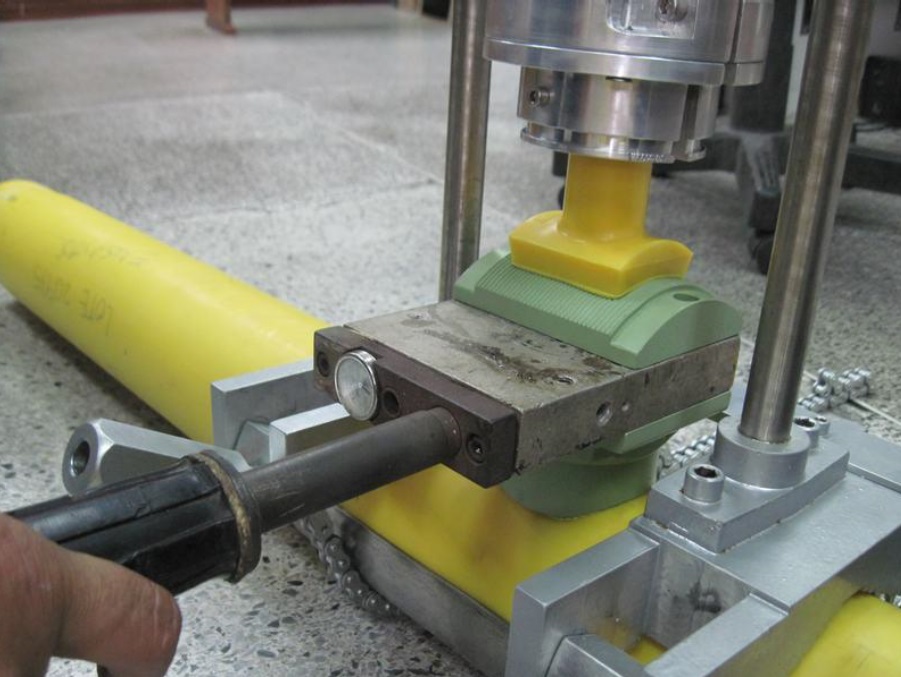
5. Place the heating tool on the main centered beneath the fitting base. Immediately move the fitting against the heater faces, apply the Initial Heat Force (see fitting label), and start the heat time. Apply the Initial Heat Force until melt is first
observed on the crown of the pipe main (Initial Heat is the term used to describe the initial heating (bead-up) step to develop a melt bead on the main pipe and usually is 3 to 5 s) and then reduce the force to the Heat Soak Force (Bead-up force) (see
fitting label). Maintain the Heat Soak Force until the Total Heat Time is complete.
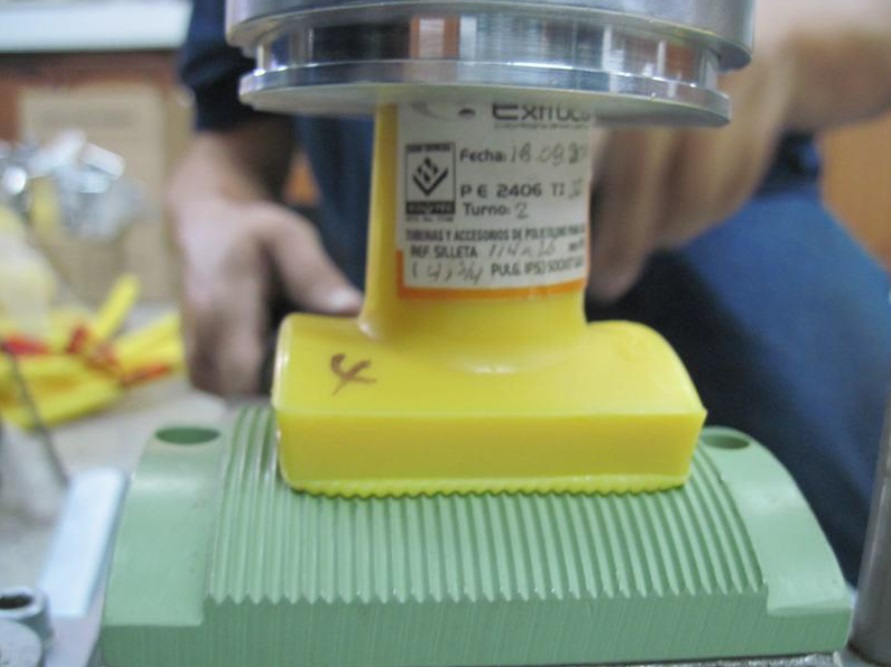
5.1. Total Heat Time ends:
(1) When the Total Heating Time expires for a pressurized IPS 11⁄4 in. (42 mm) or IPS 2 in. (63 mm) main, or (2) When a melt bead of about 1⁄16 in. (2 mm) is visible all around the fitting base for a IPS 11⁄4 in. (42 mm) or IPS 2 in. (63 mm) non-pressurized main, or a larger pressurized or non-pressurized main.
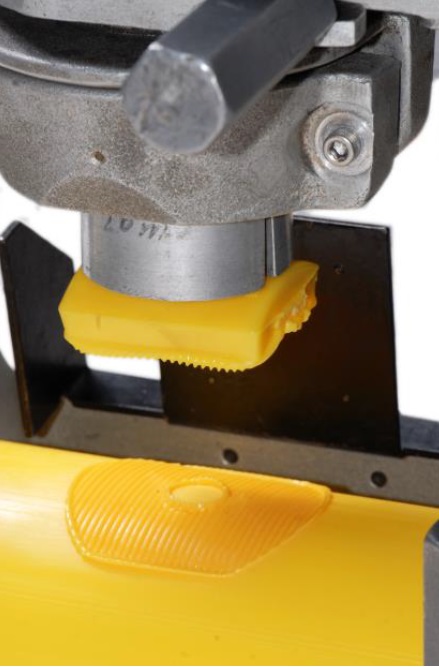
6. At the end of the Total Heat Time, remove the fitting from the heater and the heater from the main with a quick snapping action. Quickly check for a complete and even melt pattern on the pipe main and fitting heated surfaces (no unheated areas).
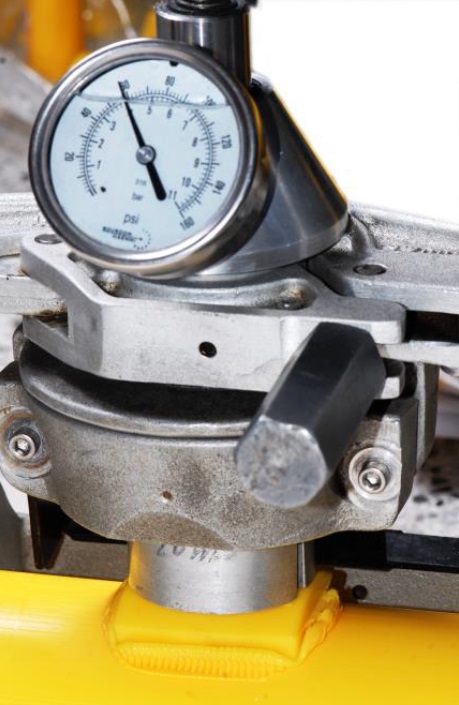
7. Fusion and Cooling: Whether or not the melt patterns are satisfactory, press the fitting onto the main pipe very quickly (within 3 s) after removing the heater and apply the Fusion Force. Maintain the Fusion Force on the assembly for 5 min on IPS 11⁄4 in. (42 mm) and for 10 min on all larger sizes, after which the saddle fusion equipment may be removed. (Fusion Force adjustment may be required during Cool Time, but never reduce the Fusion Force during cooling.)
Cool the assembly for an additional 30 min before rough handling, branch joining or tapping the main. (If the melt patterns were not satisfactory or if the fusion bead is unacceptable, cut off the saddle fitting above the base to prevent use, relocate to a new section of main, and make a new saddle fusion using a new fitting.)
Generic Saddle Fusion Parameters
Heater Adapter Surface Temperature | 500 ± 10°F (260 ± 6°C) |
Initial Interfacial Pressure | 60 ± 6 psi (4.14 ± 0.41 bar) |
Heat Soak Interfacial Pressure | 0 psi |
Fusion Interfacial Pressure | 30 ± 3 psi (2.07 ± 0.20 bar) |
Total Heating Time on Main—11⁄4 in. IPS Pressure Main | 15 s max |
Total Heating Time on Main—2 in. IPS Pressure Main | 25 to 35 s max |
Total Heating Time on non-pressure 11⁄4 in. IPS, 2 in. IPS mains,and on pressure or non-pressure 3 in. IPS and larger mains. | Look for a 1⁄16 in. (1.6 mm) bead around the fitting base |
Visual Inspection
Visually inspect and compare the joint against visual inspection guidelines. There shall be three beads, a melt bead
around the fitting base, a bead on the main from the edge of the heating tool, and a main pipe melt bead. The fitting and pipe melt beads should be rounded and about 1⁄8 in. (3 mm) wide all around the fitting base. The heating tool edge bead should be visible all around the fitting base, but may be separate from the main pipe melt bead.
The saddle fusion joint in unacceptable for use if visual bead appearance is unacceptable or if the melted surfaces were unacceptable. To prevent use, cut the fitting off at or just above the base.
NOTE 11—Look in the lower right hand corner of the fitting label for the forces required for that fitting in pounds force (Initial Heat Force/Heat Soak Force/Fusion Force) (for example, 180/0/90).
Acceptable Visual Appearance
Proper alignment, force and melt.
Proper surface preparation.Unacceptable Visual Appearance
Improper alignment.
Fitting offset from melt pattern.Unacceptable Visual Appearance
Over-melt of fitting and main.
Possible over-pressurization of fitting on main.Unacceptable Visual Appearance
Under-melt of fitting and main.
Fitting offset from melt pattern.
Possible under-pressurization of fitting on main.
DETERMINING SADDLE FUSION FORCE IF LABEL IS NOT PRESENT
When the saddle fusion fitting does not have a label to show the initial heat force (IHF) and the fusion force (FF), use
the following formulas to determine the forces required.
IHF 5 L 3 W – ~0.785 3 d2! 3 60
Determining IHF and FF:
IHF 5 0.785 3 ~D2 – d2! 3 60
IHF is determined by multiplying the area of the saddle fitting base by 60 psi, the initial interface pressure. For rectangular base saddle fittings, the fusion area is the base length times the base width less the area of the outlet hole.
Base curvature and corner radii are ignored. For round base saddle fittings, the fusion area is the area of the base outside diameter less the area of the outlet hole. Base curvature is ignored.
where:
IHF = initial heat force, lb,
L = rectangular base length, in.,
W = rectangular base width, in.,
d = outlet hole inside diameter, in., and
D = round base outside diameter, in.
FF is one-half of IHF:
FF = IHF/2