ABOUT FUSION PIPE
BLOG / NEWSLETTER
TECHNICAL STANDARDS PARAMETERS
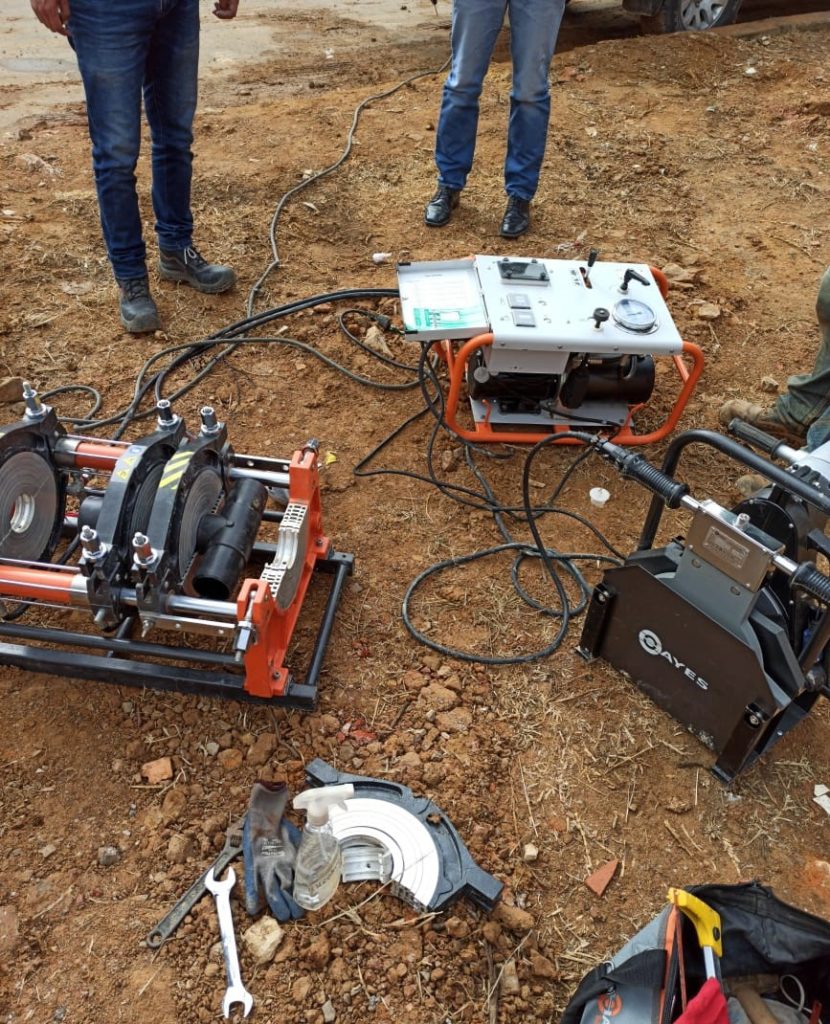
ABOUT APPROVALS AND STANDARDS
Our welding equipment is designed and manufactured according to the American international standard ASTM F2620 – 13. We have a specialized team with knowledge in fusion procedures and maintenance experience. Hayes is committed to providing quality products and customer satisfaction throughout all lines of business.
This machine can provide the fusion service for many years if it operates carefully and correctly and attends all preventive maintenance on time.
AMERICAN (STANDARD INCHES PIPE)
ASTM F2620 for HDPE
GERMAN (METRIC PIPE)
DVS 2207-1 for PE-HD | DVS 2207-11 for PP | DVS 2207-15 for PVDF
Download HAYES User’s manuals for plastic pipe welding
1 SOCKET FUSION HY
1.1 SOCKET FUSION CG
2 MANUAL BUTT FUSION
2.1 HYDRAULIC BUTT FUSION
3 ELECTROFUSION
4 SADDLE FUSION
University- Basic concepts
Welding terminology
T = Time
P = Pressure
B = Bead size
Pipe terminology
ND = Nominal Diameter
ID = Internal Diameter
OD = Outside Diameter
T = Thickness
NP= Nominal Pressure
SDR = Standard Dimensional Ratio
Relation between the Outside diameter and Thickness of the wall
Pressure terminology
PSI= Pound square inches
MPa= Mega Pascal
1 MPa= 10 Bar = 145 PSI = 1 N/mm² = 100 N/cm²
1 In² = 6.4516 cm²
1 cm² = 100 mm² = 0.155 In²
1 mm²= 0.01 cm² = 0.00155 In² = 0.00001076 Ft²
1 mm = 0.1 cm = 0.03937 In = 0.7854 mm² = 0.001217 In²
DRAG = Drag pressure
TEPA = Total Effective Piston Area
Celsius to Fahrenheit Chart Conversion
1°C = 33.8 °F
260°C = 500 °F
Applicable International Standards
ASTM F 2620 (United States)
Socket fusion Temperature
490 – 510°F (254 – 266°C)
Butt fusion Temperature
400 – 450 °F (204 – 232 °C)
Applicable International Standards
BUTT FUSION
ASTM F 2620 (United States)
IFP: 75 PSI = 0.517 Mpa = 0.517 N/mm² = 51.71 N/cm²
(Average 60 – 90 PSI)
IFP MIN (60 PSI = 0.41 Mpa = 0.41 N/mm² = 41 N/cm
IFP MAX (90 PSI = 0.62 Mpa = 0.62 N/mm² = 62 N/cm
Temperature: 204 – 232 °C | (400 – 450 °F)
DVS 2207 – 1 (Europe)
IFP: 21.76 PSI = 0.15 MPa = 0.15 N/mm² = 15 N/cm²
Temperature: 200 – 220 °C | (392 – 428 °F)
How to calculate Pressure Gauge according to the ASTM F 2620 American Standard?
(PG) = Pressure Gauge
PG = IFP*Ap + DRAG
TEPA
IFP = Interfacial Pressure
ASTM F2620 › IFP = 0.41 – 0.62 MPa / 60 – 90 PSI
DVS 2207 › IFP = 0.15 MPa / 21.75 PSI
Ap = (Pipe Area)
AP = (OD – T) * T * л
T = OD SDR = OD
SDR T
Л = 3,14
TEPA = Total Effective Piston Area
DRAG = Drag pressure
LEARN WITH HAYES
- BUTT FUSION PROCEDUREHAYES Manual Butt Fusion Machines COMBAT Series OPERATOR’S MANUAL A manual is only a manufacturer´s guide. It does not take… Read more: BUTT FUSION PROCEDURE
- SOCKET FUSION VISUAL APPEARANCE GUIDELINEAmerican National Standard – ASTM F2620 Acceptable Visual Appearance Melt bead flattened by cold ring. No gaps or voids. Good… Read more: SOCKET FUSION VISUAL APPEARANCE GUIDELINE
- SOCKET FUSION PROCEDUREHAYES Socket Fusion Pipe Welder HY PRO Series USER’S MANUAL A manual is only a manufacturer´s guide. It does not… Read more: SOCKET FUSION PROCEDURE
- HDPE PIPE APPLICATIONS AND FEATURESHDPE PIPE FEATURES THERMOPLASTIC PIPE VS TRADITIONAL PIPING SYSTEMS Leak-Proof: HDPE pipe can be joined by thermal fusion to form… Read more: HDPE PIPE APPLICATIONS AND FEATURES
- HDPE PIPE SIZE CHART CONVERSION (IPS/DIPS/mm)IPS PIPE SIZES (INCHES) – (Iron Pipe Size based) Iron pipe size, or IPS, is the original pipe sizing system from the… Read more: HDPE PIPE SIZE CHART CONVERSION (IPS/DIPS/mm)
- SADDLE FUSION PROCEDUREPROCEDURE / APPLICATION The saddle-fusion procedure involves melting the concave surface of the base of a saddle fitting, while simultaneously… Read more: SADDLE FUSION PROCEDURE
- ELECTROFUSION PROCEDUREThe main difference between conventional heat fusion and electrofusion is the method by which the heat is applied. ELECTROFUSION is a simple… Read more: ELECTROFUSION PROCEDURE
- BUTT FUSION MACHINE | WHAT YOU NEED!Hydraulic and Manual Butt Fusion Machine PROCEDURE / APPLICATION The principle of Butt Fusion joining of HDPE or PPR pipe… Read more: BUTT FUSION MACHINE | WHAT YOU NEED!
- SOCKET FUSION TOOLS | WHAT YOU NEED!PROCEDURE / APPLICATION The socket fusion technique consists of simultaneously heating both the external surface of the pipe end and… Read more: SOCKET FUSION TOOLS | WHAT YOU NEED!
- NEW HAYES SOCKET FUSION IRONDESCRIPTION The HAYES HY PRO Series is the new digital socket fusion pipe welder (heating tool) that is suitable for… Read more: NEW HAYES SOCKET FUSION IRON
- THE MAIN FUNCTION OF THE COLD RINGCOLD RING ALSO KNOWN AS ROUNDING CLAMP OR LOCKING PLIERS FOR SOCKET FUSION PIPE PROCEDURE According to the ASTM American… Read more: THE MAIN FUNCTION OF THE COLD RING
- ELECTROFUSION (HY) VIDEO TUTORIAL | SPANISH VERSIONThis video will show you how easy is to weld plastic pipes HDPE with an HY electrofusion machine.
- ELECTROFUSION (RITMO) VIDEO TUTORIAL | SPANISH VERSIONThis video will show you how easy is to weld plastic pipes HDPE with a RITMO ELEKTRA 400 electrofusion machine.
- PE PIPE SOCKET FUSION TIME CYCLESAMERICAN NATIONAL STANDARD – ASTM F2620 POLYETHYLENE Temperature: 490 – 510 °F / 254 – 266 ℃ PE80 MDPE Medium… Read more: PE PIPE SOCKET FUSION TIME CYCLES
HDPE PIPE APPLICATIONS
- Natural gas distribution
- HVAC and mechanical systems
- Fire suppression systems
- Geothermal Installations
- Potable water delivery
- Greywater and sewer lines
- Drain
- Irrigation
- Mining
- Slip lining
- Reclaimed water
HDPE PIPE FEATURES
THERMOPLASTIC PIPE VS TRADITIONAL PIPING SYSTEMS
- Leak-Proof: HDPE pipe can be joined by thermal fusion to form a joint that is as strong as the pipe itself and is leak free. Thermal fusion eliminates potential leak points every 8-20 feet commonly found with Concrete, PVC and Ductile Iron pipe. Leak proof joints also eliminate infiltration and exfiltration problems experienced with other pipe joining methods. Since fused joints are self-restraining, costly thrust restraints or thrust blocks are not required.
- Corrosion and chemical resistant: HDPE pipe will not rust, corrode, tuberculate or support biological growth and are resistant to chemical abrasion. It is the material of choice in harsh chemical environments. HDPE pipe has a smooth ID and maintains its flow capability over time – Hazen Williams C Factor remains 150, even after years of use.
- Flexible and fatigue resistant: HDPE pipe can be bent to a radius 25 times the nominal pipe diameter. This can eliminate many fittings required for directional changes compared to piping systems made from other materials. In addition, the flexibility of HDPE pipe makes it well suited for dynamic soils and areas prone to earthquake. HDPE pipe for pressure applications can accept repetitive pressure surges that exceed the static pressure rating of the pipe. Thermoplastic pipes can withstand common damages, vibrations and pressure surges.
- Lightweight and impact resistant: HDPE pipe is much easier to handle and install than heavier, rigid metallic or concrete pipe, allowing for cost advantages in the construction process. It is structurally better able to withstand an impact than other pipe materials, especially in cold weather installations when other pipes like PVC are prone to cracks and breaks.
- Easy to install: Flexibility and leak free joints allow for unique and cost effective methods of installation of HDPE pipe that the rigid Concrete, PVC and Ductile Iron pipes can’t use. These alternate installation methods (Horizontal Directional Drilling, Pipe Bursting, Sliplining, Plow and Plant, Submerged or Floating Pipe) can save considerable time and money in most applications.
- Cost-effective and permanent: HDPE pipe is cost effective and has long term cost advantages due to its physical properties, heated-fused pipelines create a leak-free systems, and reduced maintenance costs or repair needs, and conserve resources. Thermoplastics pipes, like Polyethylene (PE) are expected to last up to 100 years – saving replacement costs.
- Seamless: Fused thermoplastic pipes create a monolithic pipeline with less mechanical transitions, meaning less opportunities for leaks.